5 Ways to Avoid Misclassifying Your Shipment
Admin • August 17, 2020
This is a subtitle for your new post
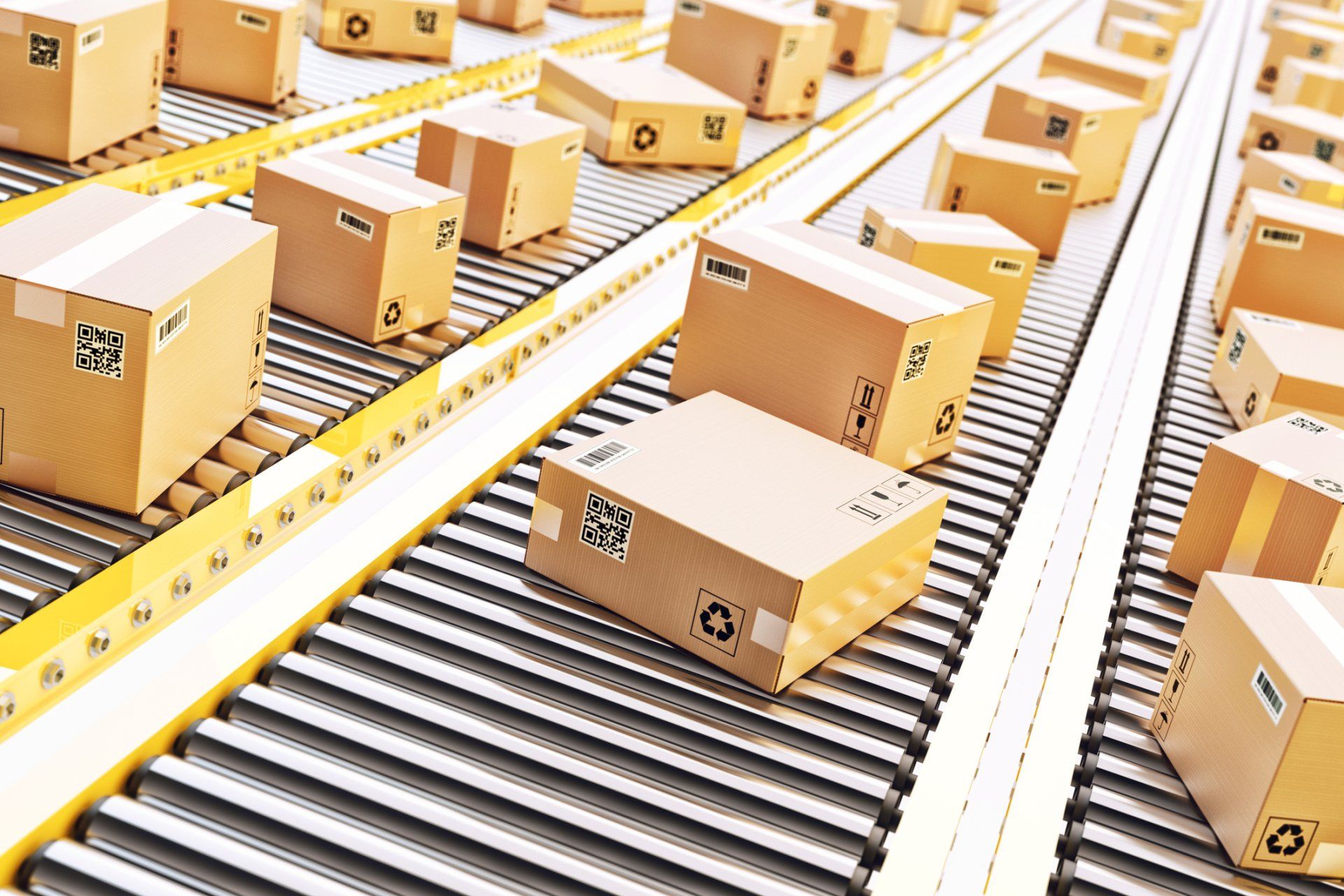
When using a Carrier to transport your products, it is crucial to accurately classify your shipment. Categorizing your load incorrectly or providing incomplete information can lead to a host of accessorial charges — extra costs and fees that are easy to avoid or budget for appropriately — if you're aware ahead of time.
When you're shipping less than a full semi truck's trailer load, you'll fall under LTL (less than truckload) standards and regulations, so it's necessary to check the rules on your shipment size before you begin. Here are a few tips to avoid some fees on your next shipment — or at least know they're coming and budget accordingly.
1. Give All Information
Make it a priority to communicate and document any details of your shipment, even if you don't think it's necessary. The size and material of the load are understood as pertinent details, especially if you are shipping hazardous or fragile materials, but include any information you can think of.
Size and density are essential to choosing a shipping class, but a lot of other factors play into your shipping class as well. Consider distance, time constraints, hazardous or fragile components, how easy it will be to stow, and the value of the shipment before choosing the class.
2. Measure, Don't Guess
You may be able to tell exactly how much something weighs or the specific dimensions of your shipment, but you should still run the numbers to make sure you're classifying your LTL load accurately. Density, or weight divided by volume, is imperative to determine in which class your product belongs. For something this important, you need measurements, not estimates.
Giving the correct measurements the first time will save you money and time in the long run. If the transporter notices a significant difference, they will have to remeasure the weight, size, and density of your shipment - all of which are extra charges you can easily avoid.
3. Check The Supply Chain
If you have a bill much higher than you were anticipating, look at the itemized invoice and backtrack on the shipment. Look down the line of people involved with the shipment and make sure that everyone is working from the same details and has the same information as the rest of your crew. This takes time, and good communication skills to dispute any mishandling of information on the supply chain.
4. Work With Professionals Who Have Your Back
Choosing a 3rd Party Logistics company to manage your LTL shipment supply chain is the simplest and easiest way to ensure you’re saving as much money as possible. JBS Logistics has over 30 years of experience working on behalf of customers with a carefully selected network of certified Carriers. Not only does JBS remove your stress by managing all the steps listed above, but we go deeper into the process to protect you and your products.
Partner with a professional 3PL to protect your interest and your LTL shipments. Contact JBS Logistics
today